So after making putting together the 3d printed coral bandsaw and learning about BLDC motors I found myself asking what other projects use these incredibly powerful and tiny motors? I found a motor part available on printables.com and found the full model was available for a 3d printable vehicle at www.3dsets.com. Not only are these 3d printable model cars very articulated they are also setup to be RC cars! I have never built or raced the serious RC cars, my experience with them was the cheaper kind you would find a drug store. I was itching for another 3d printable build and this seemed like a great way to learn about those more "serious" RC cars and give me a long build that would take a bit of organization and planning to pull off.
I browsed their vehicles and the Buggy V7 spoke to my heart and soul like none of the others. It is clearly inspired on the Baja bugs that are popular in Southern California and has a really fun juxtaposition of the dorky Volkswagen Beetle with Mad max dune buggy. I purchased the files and started reading the manual while trying to decide how to design the livery.
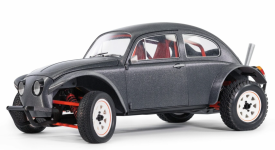
There is a lot of hardware and electronics needed for the build so I started off by ordering the recommended items from the provided BOM wherever I could find them and a kit from www.RCprinter.com. I found RCprinter from a google search but I was happy to support a small hobby business. The seller did a great job of labeling all the fasters and parts. They even have a YouTube channel with videos of the assembly.
I browsed their vehicles and the Buggy V7 spoke to my heart and soul like none of the others. It is clearly inspired on the Baja bugs that are popular in Southern California and has a really fun juxtaposition of the dorky Volkswagen Beetle with Mad max dune buggy. I purchased the files and started reading the manual while trying to decide how to design the livery.
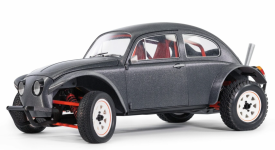
There is a lot of hardware and electronics needed for the build so I started off by ordering the recommended items from the provided BOM wherever I could find them and a kit from www.RCprinter.com. I found RCprinter from a google search but I was happy to support a small hobby business. The seller did a great job of labeling all the fasters and parts. They even have a YouTube channel with videos of the assembly.