While working on the cutting board holder, I'm bending my test pieces until they break, and am usually finding that they delaminate along the side walls. I don't think this is a printer calibration problem, since I don't have this problem on prints that aren't being pushed to breaking, but is there anything I can do to prevent this, aside from printing in another orientation (which I'm not super wanting to do)?
Some examples:
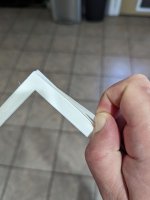

Some examples:
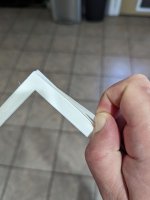
